Power Transmission Equipment
Power Transmission Equipment
The Power Transmission Equipment online mechanical maintenance training course covers belt drives, chain drives, gears and gear drives, adjustable-speed drives, shaft alignment, shaft coupling devices, and clutches and brakes. This course has no prerequisites. Power Transmission Equipment is available in online maintenance training and course manual formats.
Subscribe & Unlock Full Access
Gain immediate access to our library of expert-led training courses, labs, and support.
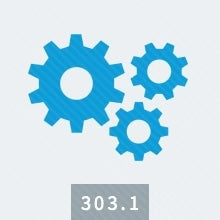
-
Description:
The Power Transmission Equipment online mechanical maintenance training course covers belt drives, chain drives, gears and gear drives, adjustable-speed drives, shaft alignment, shaft coupling devices, and clutches and brakes. This course has no prerequisites. Power Transmission Equipment is available in online maintenance training and course manual formats.
-
Included Courses:
Lesson 1 - Belt Drives
Topics:
V-belts; Timing and flat belts; Sheaves; Pulleys; Installation
Learning Objectives:
– List the factors that affect the power transmitted by a belt drive.
– Name the main components of a belt drive.
– List the standard V-belt designations.
– Explain the reason for using group belts.
– Describe installation and replacement procedures for V-belts
Lesson 2 - Chain DrivesTopics:
Terminology; Roller, double-pitch, leaf, and silent chains; Cast drive chains; Sprockets; Installation
Learning Objectives:
– Explain the differences between chain drives and belt drives in transmitting power.
– Explain how a roller chain drive works.
– Describe the construction of offset roller chain.
– Explain the differences between sprocket types A, B, and C.
– List the steps in installing a chain drive.
Lesson 3 - GearsTopics:
Gear definitions and drives; Tooth contour and diametral pitch; Spur, helical, single-, double-cut, herringbone, bevel, and worm gears; Maintenance
Learning Objectives:
– Define the following terms used to describe gear drives: pitch circle, pitch diameter, working depth, tooth face, tooth flank.
– Calculate the diametral pitch of a gear.
– List advantages and disadvantages of helical gears.
– Explain the differences between herringbone gears and double-cut helical gears.
– Define the following terms used in discussing worm gears: worm lead, worm lead angle, normal worm pitch, worm axial pitch.
Lesson 4 - Gear DrivesTopics:
Shaft-mounted, worm-gear drives; Miter-gear boxes; Gear drive installation, maintenance, and definitions; Concentric, parallel, right-angle, vertical-shaft gear drives
Learning Objectives:
– Explain how additional speed reduction can be obtained with shaft-mounted gear drives.
– Describe a worm-gear drive and a miter-gear box.
– Give a general explanation of gear drive installation and maintenance.
– Define mechanical power, thermal power, and overload capacity.
– Explain what determines the service factor of a gear drive.
– Describe a concentric-shaft gear drive and a right-angle-shaft gear drive.
– Explain how parallel-shaft gear drives are lubricated.
Lesson 5 - Adjustable-Speed DrivesTopics:
Belt- and disk-type adjustable-speed drives, Roller-type, hydraulic, and electric adjustable-speed drives
Learning Objectives:
– Identify the main criteria for selecting adjustable-speed drives for industrial plants.
– Explain the operation of a variable-speed belt drive.
– Describe how to control variable-speed drives.
– Describe the belts and chains used for variable-speed drives.
– Explain the operation of a roller-type variable-speed drive.
Lesson 6 - Shaft AlignmentTopics:
Geometry of shaft alignment; Preparation; Reverse-indicator method; Aligning multiple machines; Face-rim, long-span, and laser alignment
Learning Objectives:
– Determine the corrections needed to align two machines, using the reverse-indicator method.
– Determine the corrections needed to align two machines, using the face-rim indicator method.
– Determine the corrections needed to align three machines on a common centerline.
– Determine the corrections needed to align two machines separated by a long floating shaft.
– State at least three advantages of using laser alignment equipment over using dial indicators.
Lesson 7 - Shaft Coupling DevicesTopics:
Solid, jaw, molded-rubber, chain, gear, metal-disk, shear-pin, torque-limiting, brake-wheel, floating-shaft, spacer, insulated, and other couplings
Learning Objectives:
– List three functions usually performed by a coupling.
– Describe two types of jaw couplings.
– Name an application for molded rubber couplings.
– State an advantage of chain couplings.
– Explain the operation of a shear pin coupling.
– Describe a torque limiting coupling.
– Name an application that involves a floating shaft.
– Describe a limited end float coupling.
– List advantages and disadvantages of spacer couplings.
Lesson 8 - Clutches and BrakesTopics:
Jaw, friction, torque-limiting, tooth-type, centrifugal-type, overrunning, electric, and fluid clutches; Friction shoe, disk, electric brakes
Learning Objectives:
– Explain the purposes of a clutch.
– Describe the operation of a friction clutch.
– Explain the need for overrunning clutches.
– Name at least one application for an electric clutch.
– Explain how a fluid clutch works.